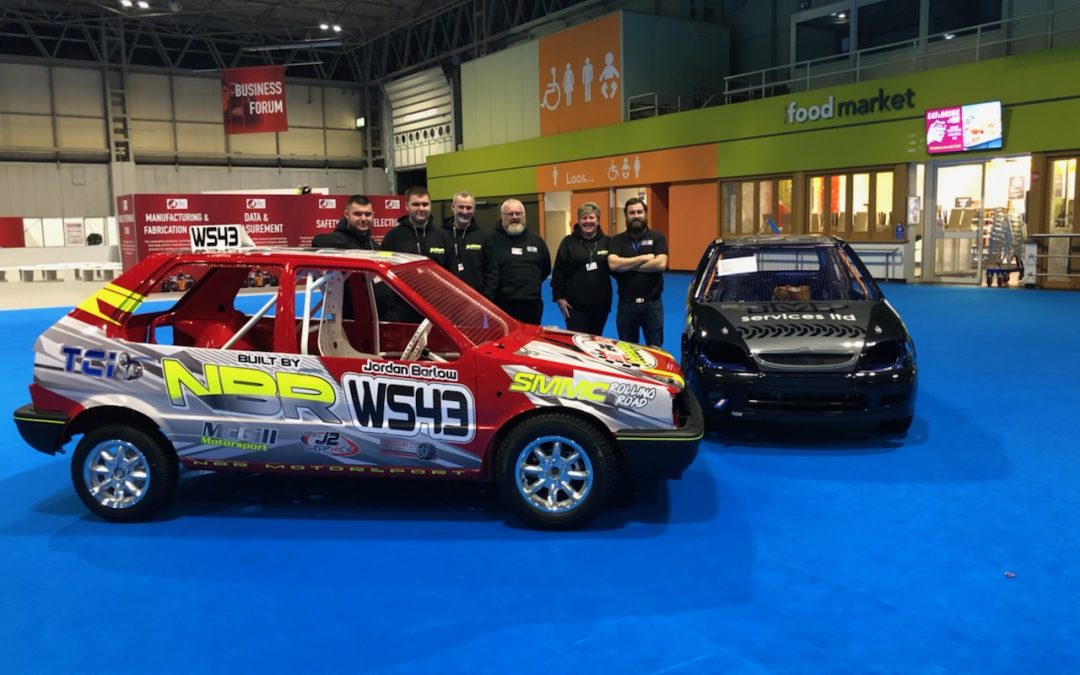
Major investment with ETG as Bowmill launches new aerospace manufacturing plant
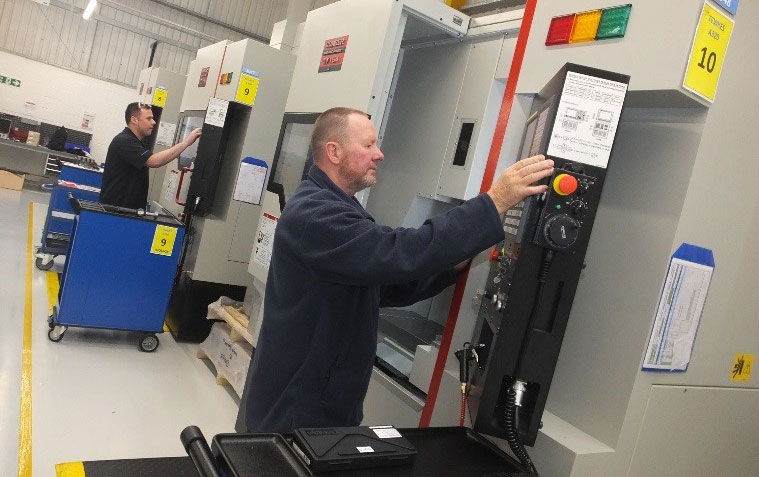
In its design and fitting-out of a new bespoke factory designed to manufacture Airbus landing gear kits, Poole, Dorset based aerospace engineering solutions specialist Bowmill Engineering Ltd has opted to purchase 8 brand new machining centres from the Wellesbourne, Warwickshire based Engineering Technology Group (ETG).
Bowmill’s new high volume plant is situated in Tewkesbury, Gloucestershire, close to four of its major landing gear customers based in nearby Gloucester and itself in the centre of a growing manufacturing conurbation.
At its main factory in Poole, Dorset where it operates a dedicated KANBAN facility for Airbus landing gear kit production, Bowmill has been manufacturing A320 and A330 landing gear kits since 2002 as well as complex components and assemblies for other OEM’s. Operating in a competitive, cost-down environment necessitates they “stay ahead of the game” in the words of managing director Nick Epps and to that end, machine tool investment is both extensive and ongoing.
In Poole, Bowmill currently operates a major component machining set-up for Class 1 critical parts with the cornerstone being an ETG supplied Chiron FZ15FX, 5 axis machining centre.
The FZ15FX has enormous ability and high speed machining capacity and is claimed by Chiron to be among the best machining centres of its class in terms of speed, compact construction, stability and reliability. The heart of its technology is the CHIRON basket tool changer which offers high positioning accuracy, since the travelling column does not need to change its X – Y position during a tool change.
This machining centre was installed following an objective review of Bowmill’s manufacturing capabilities in which the advantages of progressing from multi-operation methods using a low cost machine base to an advanced technological manufacturing system were thoroughly assessed.
A consequence of its installation has seen Bowmill able to adopt the ‘slave link’ machining technique whereby billet materials used for creating larger components such as brackets have cavities machined out as solids as opposed to milling out with consequent scrap. With slave link, the ‘scrap’ billet is used to manufacture another smaller component (or components) considerably reducing raw material waste.
As a consequence, the Chiron was installed and has reduced machining times by 21%, defects by 7% and reduced raw material usage by 28%.
After 18 months successful operation the decision was then taken to automate the process with the addition of an FZ12 Flexcell Uno automated manufacturing/robotic system. This enabled a further 12 of the A320 prismatic kit components to be moved to the machine with lights out operations.
Read the full story at www.engtechgroup.com
Related Articles
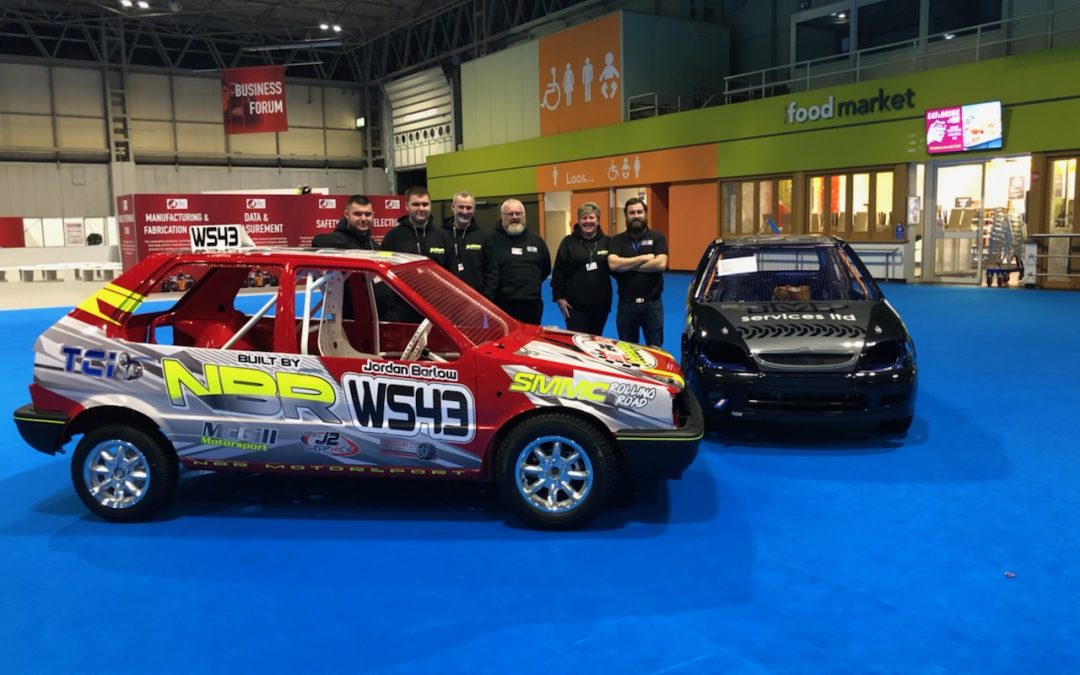